Today I started off just wanting to clean my garage windows and ended up with an A/C installed in the garage.
Once I started to clean the glass I noticed that I better prime the sill to protect the wood from more water damage.
Once I had the sashes out I decided to prime & reglaze them too. I got to put the high speed drill & putty cutter/chaser to use - it does a much better job using a high speed drill.
So once the putty & glass was removed I scrape the sills and primed them too.
Then I got to thinking - first was I should really mount them on hinges so they could open and maybe put in a screen to keep the bugs down. Then I though, I have that 5000 btu A/C that is still sitting in the basement
(I bought it used last year and Calvin hasn't shown any interest in helping me with running a new circuit to the front bedroom to power it) so I decide if it would fit, I would install it in the garage. It shrinks down to 19 inches and the opening on the garage windows are 20 - bingo.
While the paint is drying I head out for hardware - hinges for the garage windows & plumbing parts for the cistern pumps.
We get an inch and a half of rain but my cistern didn't fill up that much - damn now I am going to have to clean the gutters & drainage pipes. More on the cistern job tomorrow - if it isn't raining.
Now if I ever find out who shot BB's at the garage windows (plus several others around my house...) - 4 of the 8 panes had holes, and one was cracked. I only broke one removing the glass but it already had a BB hole in it so that doesn't count. I installed three good panes and one with a hole not cracked (I am saving the one with the BB hole along the edge to serve as the model for the 5 new panes I'll have cut soon to finish the other sash.
I popped the A/C in - cut some scrap 3/4 plywood - glued some white plastic to the exterior and mounted the other sash on hinges. So now I got A/C - well it's an uninsulated garage but it will likely be better than having the doors open where Daisy can escape and bugs can get in - it's not like I am planning on leaving it on 24/7.
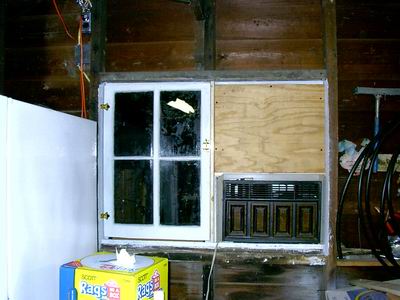